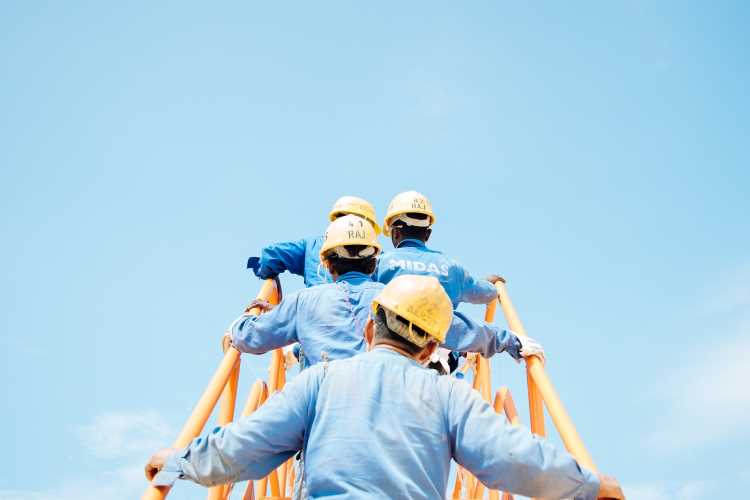
Manufacturing is a key contributor to the economic development of a nation, and capital goods are at the core of the manufacturing activity. The capital goods industry is called the mother of all manufacturing industries. The sub-sectors of capital goods include agro & food processing machinery, machine tools, industrial machinery, process plant equipment, construction & mining equipment, electrical equipment, textile machinery, and printing & packaging machinery. It is apparent that it serves all sectors of the manufacturing economy right from mining to machining, harvesting to handling, and processing to packaging.
Till the time of independence, the capital goods sector was almost non-existent in India. To reduce dependence on foreign countries for basic raw materials such as steel, aluminium, machine tools, processing machinery, and power plant equipment, a push for self-reliance was given by the government under the second five year plan to set up industrial units to produce them indigenously. To meet the ambitious plan for the production of steel, large integrated plants were planned under Hindustan Steel Ltd/ SAIL. Simultaneously another PSU, namely HEC Ltd, was set up to produce machinery for these steel plants and other machinery. Hindustan Machine Tools was set up to locally produce various machine tools such as CNC lathe, milling, drilling, shaping machines, metal forming presses, pressure die casting machines, and plastic injection moulding machines required for manufacturing processes across sectors.
READ I How can India correct trade imbalance with China
The government also established a factory in Bhopal for the manufacture of heavy electrical equipment for power generation that was further expanded under BHEL with more units to offer a complete package for setting up power generation units. These steps initiated in 1950s and 60s could be described as attempts to establish a modern capital goods (CG) industry. However, it may not be construed to suggest that the private sector in India was a non-player in the segment. Several units in private sector have contributed substantially to the growth of this industry in India. A majority of these units are in the SME sector.
The capital goods industry had an overall production figure of $35 billion in 2018 -19. It provides 1.4 million direct and 7 million indirect jobs. The industry is dominated by the electrical and power plant equipment sector with about 69% of the output. The growth of India’s capital goods sector has been sluggish in the recent past at around 2.7% in 2018-19. Between 2010 and 2015, it grew at a modest rate of 2%, compared with the GDP growth rate of 7%. With such a sub-scale performance, India has failed to be a major player in the global market and has a small share of just 0.8%. Even the contribution of this sector is only 1.9% of India’s GDP compared with 4.1% and 3.4% for China and Germany, respectively. The capital goods imports into India increased at a rate of 9.8% per annum between 2010 and 2015. The share of imports in the Indian capital goods market increased to 40% since 2010. Capital goods are now the fourth largest import category after crude oil, electronics, and gold.
READ I Venture capital sources dry up for Indian start-ups
Policy Initiatives in capital goods sector
India’s capital goods sector is relatively underdeveloped for the fifth largest economy in the world. The current situation is the result of the protection provided under the license permit raj. The domestic manufacturers were unprepared to grab the opportunity offered by the economic reforms in 1991 to become global players, following the feats of the auto components industry and the pharmaceuticals industry. After the removal of the trade barriers, domestic producers opted for more advanced machines available at a competitive price from countries like Japan, Italy, Taiwan, and later from China. Many domestic entrepreneurs looking for production machines were lured by offers to buy used production lines at throwaway prices in east Europe and elsewhere. The economic reforms also gradually opened up the capital goods market through the FDI route, and in the year 2000, FDI up to 100% was allowed under automatic route in companies engaged in the manufacture of capital goods. However, global manufacturers of capital goods have shown limited enthusiasm in bringing capital here for setting up a production unit, as the table below indicates:
During the same period, sectors like services, computer hardware & software, telecommunication, and trade attracted 17.45%, 9.56%, 7.93%, and 5.87% of the total FDI inflows into India, revealing an explicit preference of foreign investors to India’s services sectors. Though the annual FDI inflow into India increased from $6.05 billion in 2004-05 to an impressive $73.5 billion in 2019-20, the country has not emerged as a preferred destination of global manufacturers. Industrial machinery and machine tools could only get 1.2% and 0.21% of the FDI inflows in the last 20 years. This facet of our external engagement in the industrial sector calls for an honest review of the ground realities concerning the ease of doing business in the manufacturing sector. Besides, certain provisions under the foreign trade policy such as free import of used machinery have been cited as not helpful for the development of the domestic industry.
- Nil import duty provision under the Export Promotion Capital Goods policy,
- Duty concession for capital goods under project imports, and
- FTAs with countries that have an edge over India with respect to capital goods production.
Notwithstanding the benefits of reduced capital cost for manufacturers, import of used capital goods not only affects the domestic industry, but also impacts the productivity and competitiveness of the user industries. What is suggested is a relook at the trade regime for rationalisation. However, it would not be prudent to place the entire onus on policy framework. It is the lack of dynamism of the overall manufacturing sector that is responsible for the sluggish growth of the capital goods sector in India. The manufacturing sector growth achieved in recent years was well short of the required growth rate of 12-14% to increase the share of the manufacturing sector to 25% of the GDP. The slowdown in the industrial sector witnessed in 2019 followed by COVID-induced slowdown make the target even more challenging.
READ I Atmanirbhar Bharat: Reducing dependence on China for pharmaceutical ingredients
The disappointing performance of the sector prompted the government to formulate the National Capital Goods Policy (NCGP) in 2016. The policy envisaged increasing production of capital goods from Rs 230,000 crore in 2014-15 to Rs 750,000 crore in 2025. It further envisaged increasing exports from 27% at present to 40% of the output while increasing the share the domestic market from 60% to 80%. The policy envisages improvement in technological capabilities of domestic manufacturers, increase skill level, and promote capacity building of MSMEs. These are good initiatives, but it is too early to assess the impact of the policy on the domestic industry.
Creating opportunities during crisis
With the lifting of the lockdown and the renewed focus on resuming economic activities, the industry needs to introspect for achieving competitiveness by adopting global best practices to reduce power, logistics, and production costs. Here are some ways for achieving a share in the global market befitting a large economy like India.
Greater integration into global value chain
Lockdown, travel restrictions, and social distancing norms intended to prevent further spread of the coronavirus have disrupted the global economy. The pandemic has a severe impact on international production networks that may remain for years to come. Global value chains (GVCs) have been affected in terms of the missing link of supplies. In these uncertain times, companies across the world are closely monitoring inventory positions, both in the short and the long term. To mitigate the adverse effect of another supply disruption, global manufacturers are planning to diversify their supply chain. India stands to gain from the reconstruction of the supply chain, post-COVID outbreak. Across India, over the years Chinese imports have forced the closure of many manufacturing plants, as they discovered the profit in switching from manufacturing to trading. Now, the disruptions in supply from China have provided an opportunity for Indian companies to reorient their focus on manufacturing by offering products earlier imported that have already proved their worth in the market. The size of the domestic market is large enough to scale up their production volume at a cost-effective level and join the GVCs. This will strengthen manufacturing activities and, in turn, boost the capital goods sector in India.
READ I FDI from China: India must balance strategic and economic interests
Enhancing Technological depth
Joining the global value chains can benefit the Indian economy and industry, but the participation and the gains thereof do not come automatically. It requires competency to make products at a quality and efficiency level equivalent to world standards. One of the channels for skills and technical development needed to achieve the goal is foreign direct investment. The technological competitiveness of the Indian capital goods sector is considered moderate. While some manufacturers have robust in-house capability in product design and process technology, the skill and knowhow level of most manufacturers is limited, especially of those the SME category. In India, there are around 400 manufacturers of CGs in the unorganised sector. The National Capital Goods Policy 2016 has a component to provide capital subsidy to SME units to promote the manufacturing of quality products. Also, a cluster-based approach is needed to create common facilities like testing, skill development centres and tool rooms, preferably by the Centre or state governments.
Supportive policy framework
Indian capital goods manufacturers are often out-priced by their competitors from East Asia, even when a technically competitive product is offered. Apart from in-house costs, they are at a disadvantage due to cost factors beyond their control such as raw material costs and financing costs. Just to illustrate, the cost of steel, the main input in making machine tools, and credit interest rates are much less in China, making it difficult for Indian manufacturers to compete with them. Further, for SMEs, financial assistance alone is not enough for achieving global competitiveness. Other support services are equally vital for sustained competitiveness of SMEs such as skill up-gradation training, marketing assistance and infrastructure support. Upgrading technical skills is a constant need to acquire enhanced precision, reliability, productivity, and improved energy efficiency. Establishing institutes like CMTI, Bengaluru can play a role in improving the technical competence of manpower working in product development. This will enable the SMEs to add value to the existing products, develop new products, and also take up new services for the ever dynamic market. However, to design the ecosystem for such support services, reliable statistics is essential. Largely, the statistics available on SMEs is inadequate, and not updated. While local government machinery does not always show interest in collecting and organising the data, many SMEs do not register to remain outside the formal economy, thus do not figure in the planning process.
READ I Transparent taxation: Last mile reforms can galvanise tax collections
Collaboration between academia and industry
Collaboration with the academia is desirable for the industry for solutions to production-related problems. Conducting research and development activities that are both practically relevant and scientifically correct have been a challenge for Indian universities. Globally, there are many examples of highly successful collaboration between universities, industry, and start-ups. While in India, industries rely mostly on their in-house research rather than approaching academia. It is, however, good to see a change in this approach. The department of heavy industry set up a centre of excellence on machine tools and production technology in 2016 in partnership with IIT Madras and Indian Machine Tool Manufacturers’ Association (IMTMA). This centre, Advanced Manufacturing Technology Development Centre (AMTDC), seeks to develop state-of-the-art machine tools and production technologies, impart technical education and training to its customers, and to facilitate business development and incubation. Currently, this Centre is working on projects including 5-axis universal machining centre, electrical drives for machine tool axes and spindles, hydrostatic guideways, and spindles for high precision machine tool applications.
Capital goods sector reflects economic status
The approximate value of import of capital goods in 2018-19 was $26 billion, with China topping with around 32% share. The other major sources for capital goods were Germany (10.95%), Japan (10.75%), the US (4.44%), South Korea, Italy, Singapore, the Netherlands, and Belgium. From the data, one can say that the status of development of the capital goods sector, and in particular the machine tools, fairly determines the gap in technological development between developing and developed countries. China is the leading source for import of capital goods into India, but Germany, Japan, and the US are preferred for certain categories of high precision machines despite being relatively costlier. Let us illustrate this issue with two products of different levels of technologies – machining centres and rolls for rolling mills. The technology used in multi-axis machining centres calls for a certain amount of excellence in their design and construction which may not necessarily needed in the production of rolls.
READ I NEP 2020: Towards a knowledge economy for the globalised world
Machining centres
Machining centres are used for production of large and complex parts /components of wind turbine, automobiles/railway/aerospace that requires highest precision and productivity. In respect of machining centres, the market share of local producers is much less. Internationally, Japan and Germany are strong in technology while China has the advantage of competitive prices. The import data for machining centres show that Japan, and not China, remains the preferred source with a share of 44%.
Metal-rolling mills and rolls
The rolling process is the most common industrial process, which is used for making large length cross-sections like angles, sections, foils, sheets, and plates of steel and aluminium for structures. India imported rolls worth $533.59 million in 2018-19. The quantum of imports from Japan and Germany is around half of that from China which has a share of 34% in total imports. This explains the preference to a more cost-saving source.
The bottom line
The capital goods requirements in India is expected to increase in the coming years. The drivers propelling its growth are demand for infrastructure creation, capacity addition in the power generation sector, increasing coal production, ramping up of capacity of steel production, and, push for manufacturing activities. If these plans get implemented, the domestic capital goods industry is estimated to cross $100 billion production value by 2025. This scale of demand creation with mandatory standardisation can be utilized for improving technology depth and competitiveness of Indian manufacturers. It could also help in improving quality standards of the locally made machinery, otherwise Indian companies will end up becoming assemblers with low value addition. This is vital not only for stopping foreign exchange drain on imports and royalty payments, but also from a strategic point of view. Capital goods used in any production unit require long-term engagement with the manufacturer/supplier. Absence of this engagement may greatly impair the operations of local manufacturers. In this context, the overdependence on China could be a liability during war-like situations.
READ I Surviving the economic tsunami of Covid-19 recession
The transformation of Indian capital goods sector from a low-end to a high-end one will require investment in human talent as well as in research and development. Countries like the US, Germany, and China are able to produce quality capital goods because they have invested heavily in R&D, innovation and intellectual property ecosystem. The statistics in the table below explains why these countries are dominating the capital goods market globally.
The impact of the investment on R&D by companies can be gauged from the remarkable accomplishment by Chinese companies. In the mid-1990s, private-sector R&D investment in China represented only 2% of the world’s total R&D investment by companies. This share rose to 27% in 2017. While global R&D expenditures have doubled during the last 25 years, India’s share in global R&D expenditures increased from 1.8% to 2.9%.
Thus, a combination of initiatives including investment in R&D, facilitating policy atmosphere, global quality standards, a public procurement policy, skill development, and supporting marketing mechanisms can create an environment for fostering growth in the capital goods sector. Overall, it will require sustained efforts by all stakeholders to accelerate demand creation and to create an efficient production mechanism.
(Krishna Kumar Sinha is an industrial policy expert based in New Delhi. He retired from Indian Engineering Services in 2017. The views expressed are personal.)
Krishna Kumar Sinha is an industrial policy and FDI expert based in New Delhi. His last assignment was as an industrial adviser in the department of industrial policy and promotion, DIPP, currently known as DPIIT, under the ministry of commerce and industry of the government of India.