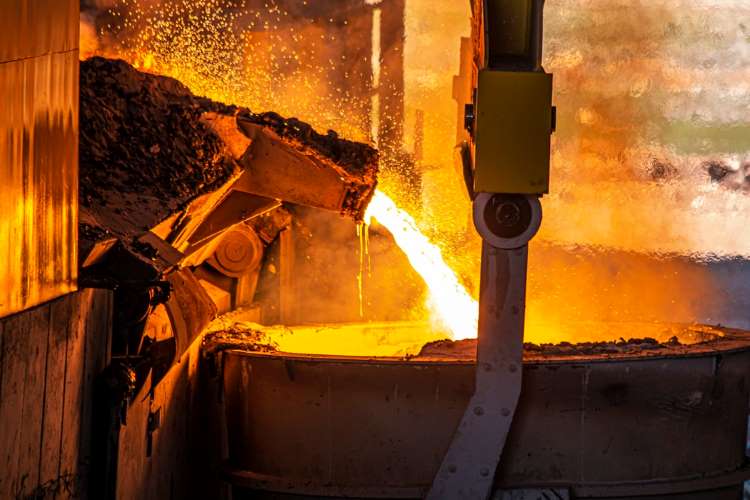
Steel industry co-products: The nation which gains control of iron soon acquires control of gold, Thomas Carlyle famously said. For a long time, steel has been an indicator of economic growth of a country. This is more so for a rapidly urbanising country that aspires for better infrastructure and wants to bridge the rural-urban gap. India is prime example for such a country – it wants to break away from low-income bracket and aspires to have 160 kg per capita of steel consumption in next 10 years from the current 74 kg per capita consumption.
It has valid reasons to think so. Steel consumption grew at the rate of 5.2% CAGR during FY16-20.The steel industry was one of the shining stars of Insolvency and Bankruptcy Code (IBC) and saw consolidation without disruption of activities of distressed assets. Steel industry witnessed fast recovery in the first wave of Covid-19 and became a net exporter in FY21. The sector also saw deleveraging and many integrated players are going ahead with expansion plans. The sector is getting support from the Union government as well as state governments through various schemes like Purvodaya, National Infrastructure Pipeline, and single window clearance.
While there is no doubt on the way forward for India, home to the second largest steel industry in the world, in expanding steel production and consumption, the policy makers should give equal emphasis to co-products for a populous country where land is getting scarce with time, where afforestation is required for offsetting carbon emissions, where forest has to be protected for maintaining its tag of one of the top 12 mega biodiverse countries and where many parts of the country are fast becoming water stressed regions.
READ I Four years of GST: Centre must simplify regime, win back states’ trust
The co-products should be seen from the perspective of opportunity and as resource for other sectors. They can very well serve as raw materials for many sectors and can reduce pressure of negative impact of fresh production. It ensures greater alignment with the path of sustainable development and circularity. Utilisation of steel industry slag prevents area required for land filling and addresses negative impact on water bodies and vegetation. Steelmaking slags are used for road construction and thus preserves sand and gravel that would otherwise need to be excavated. When co-products such as dust and scales are fed back into steel making process, it saves on natural resources and allows resource efficiency.
Steel industry co-products and their applications
Ironmaking slag and steelmaking slag: In the iron and steel making process, unwanted constituents present in the raw materials (gangue) are removed using various fluxes, in the form of ‘slag’. This removal happens during iron making (generating BF slag) and steel making (generating BOF/LD slag along BF-BOF/LDF route and EAF slag along EAF route).
Ironmaking slag
During Ironmaking in the blast furnace (BF), it is necessary to remove impurities like Silica (SiO2), Alumina (Al2O3), and other undesirable components from raw materials (iron ore, coke etc.). Limestone is added as flux in the ironmaking process to enable this removal. By reacting with the impurities, the flux lowers their melting point, making it easier to separate them from the metallic iron as BF slag. Global average generation rate of BF slag is 275 kg/tonne of crude steel (Source: World Steel Association).
Different forms of BF slags are produced depending on the methods used to cool and further process the molten slag.
Granulated Blast Furnace Slag (GBFS): Produced by rapidly water quenching the molten slag to a glassy product with little or no crystallisation. This process results in the formation of sand size fragments, usually with some friable clinker like material. The physical structure and gradation of granulated slag depends on the chemical composition of the slag, its temperature at the time of water quenching and the method of production.
Air-Cooled Blast Furnace Slag (ACBFS): Produced by pouring the liquid slag into beds and slowly cooling under ambient conditions, which forms a crystalline structured, hard, lump slag, which is then crushed and screened.
READ I MSME 2.0: A policy prescription for inclusive economic growth
Applications of BF slags
Ground Granulated Blast Furnace Slag (GGBFS), produced by crushing/milling GBFS to very fine cement-sized particles, has cementitious properties and can be used as a partial replacement for or as an additive to portland cement.
Cement and concrete: BF slag is utilised by cement manufacturers for producing portland slag cement (PSC) that is a blended cement most suitable for infrastructure projects because of its high flexural strength. It is manufactured by either inter-grinding portland cement clinker, gypsum and GBFS or blending GGBFS with ordinary portland cement (OPC) by mechanical blenders. PSC’s inherent chemistry gives it several advantages over ordinary cement. Apart from being environment-friendly, it has superior compressive strength, excellent resistance to chloride and sulphate attacks, lower risk of cracking etc.
Roads and pavements: ACBFS demonstrates good friction, stripping and wear resistance due to which it is used as a replacement of natural aggregates for road making and manufacturing paver blocks for pavements.
Mineral wool: ACBFS is a raw material for manufacturing mineral wool which is a high-quality, versatile ¬fibre suitable for a variety of applications including ceiling tiles, insulation, and cementitious reinforcement.
Manufactured Sand (M-sand): ACBFS crushed to fine aggregate size can substitute 100% of river sand in concrete and mortar applications.
READ I Covid-19 lessons: India needs cooperative federalism of the flexible kind
Steelmaking Slag
BOF/LD slag and EAF slag are the two types of steelmaking slag based on the steelmaking route – the first from the BF-BOF/LDF process and EAF slag from the EAF process.
BOF/LD slag is generated when impure iron (pig iron/ hot metal) produced by blast furnace is converted into steel in the Basic Oxygen Furnace (BOF)/ Linz–Donawitz Furnace (LDF). In BOF/LDF, lime and other auxiliary materials are added, and oxygen is blown onto the impure molten Iron to reduce quantities of carbon, phosphorous, sulphur, and other undesirable components to permissible levels. The slag thus generated is separated out and is termed BOF/LD slag. Global average generation rate of BOF/LD slag is 126 kg/tonne of crude steel (Source: World Steel Association).
Applications of BOF/LD slag
Roads and pavements: Processed BOF/LD slag is an ideal material for roads. It is used as a replacement of natural aggregates in all the layers of road making. To achieve the required specifications for this application the BOF/LD slag is generally crushed and screened, followed by weathering to limit the expansion due to free lime to within 2%. Processed BOF/LD slag has better mechanical characteristics than Natural aggregates like better resistance to fracture under pressure etc.
Fly ash bricks: The finer size fractions of BOF/LD slag is used as replacement of natural sand in manufacturing fly ash bricks (used in the construction industry). The free lime content of the slag partially replaces the lime that is added as binding material for the constituents of the bricks. The Fly Ash bricks made from LD Slag are of superior quality and greater strength than red bricks. Moreover, the production of Fly Ash bricks causes little or no pollution unlike red bricks.
Cement and concrete: Suitably processed BOF/LD slag containing free lime is used as partial replacement of limestone in clinker making which is in turn used for making cement.
PSC: Trials have found that BOF/LD slag can be potentially used as a partial replacement of BF Slag (up to 15%) for portland slag cement (PSC) manufacturing where the use of LD Slag is expected to reduce the cost of making PSC.
OPC: BOF/LD slag can also be potentially utilised in making ordinary portland cement (OPC) as a performance improver. The guidelines in IS 269 mentions its usage of up to 5%. Use of LD slag in OPC making shall reduce the cost of manufacturing OPC and improve the quality of cement.
Carbon negative concrete: Certain companies like Carbicrete have successfully developed processes for making carbon-negative concrete with ground LD/BOF slag (replacing cement) which is cured in CO2 (thus, capturing the CO2).
Hardstand: Suitably processed BOF/LD slag is used to make hardstands which are paved areas for parking heavy vehicles, and storing raw materials/finished¬ products as BOF/LD slag aggregates have better strength, abrasion and impact resistance as compared to natural aggregates.
Rail ballasts: Suitably processed BOF/LD Slag can be potentially used for making rail ballasts. CSIR-CRRI & RDSO are collaborating for a joint project for development of methodology and specifications for utilisation of steel slag as ballast material in railway track.
Soil conditioner/ fertilizer: Suitably processed BOF/LD slag is used as a key raw material for making soil conditioner/fertilizer as it is rich in calcium (Ca), sulphur (S), iron (Fe), magnesium (Mg), silicon (Si) and other fertilizer components.
Marine forest restoration: According to some studies, suitably processed BOF/LD slag may potentially be used for restoration of marine forests.
Concentrated solar power: There have been trials on exploring the possibility of using BOF/LD slag as valuable low-cost heat storage material for CSP applications under the ‘REslag Project’ funded by the European Union’s Horizon 2020 Programme.
The complete utilisation of BOF/LD steel slag is an issue that has plagued the steel industry for years and continues to be a major concern due to several reasons. BOF/LD slag contains free lime which expands in contact with moisture/ CO2 from the atmosphere which restricts its use in various potential applications. It is also considered an environmental hazard due to leaching which causes soil, surface water and ground water contamination. The substantial volume of the LD slag generated (15% of the volume of steel produced) compounds the problem and if left unutilised, the major portion of the slag is dumped in open areas which could have been used for more productive applications.
EAF Slag is generated when impure iron containing metal scrap and/or direct reduced iron (DRI) is converted into steel in an electric arc furnace (EAF). Global average generation rate of EAF Slag is 169 kg/tonne of crude steel (Source: World Steel Association).
Applications: Like BF and BOF/LD slag, EAF slag can be used for making cement, concrete, roads, pavements etc. There are other co-products like dust and sludge, process gases, chemicals like coal tar, ammonia, phenol, sulphuric acid, etc., generated during coke making which have multiple useful applications.
There has been extensive research by private sector steel industry and government agencies to develop applications of co-products. There have been deliberations on financial incentives in terms of lower classification in railways for transport, lower GST, use of digital technologies for mapping demand of co-products vis-a-vis resources, collaboration of user and generating sectors. However, some of these are yet to bear fruit.
While the focus has always been on steel production and consumption, policy makers should give equal emphasis to effective utilisation of co-products from steel industry to avoid pressure on land and water for its disposal, and at the same time facilitating their use as raw materials for other sectors.
(Pankaj Satija is Chief Regulatory Affairs at Tata Steel. Views expressed are his own and not necessarily represent the views of the company.)
The author is Executive Incharge, Ferro Alloys and Minerals Division, Tata Steel Ltd. The views expressed in this article are of the author and not necessarily those of the company he is associated with.