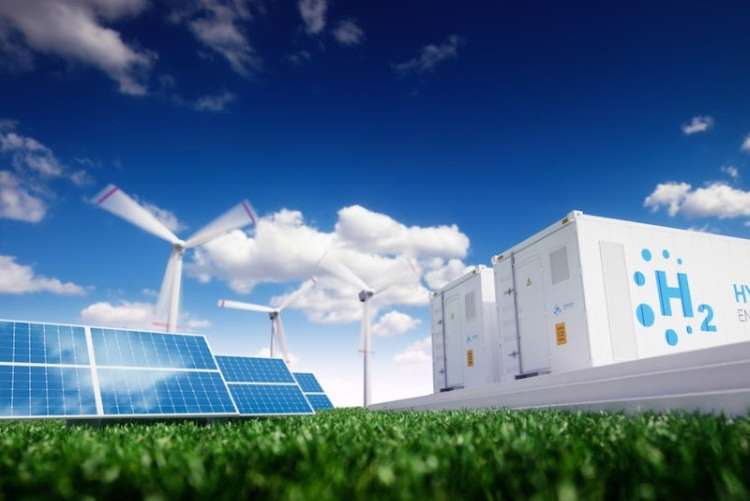
The race to establish a global green hydrogen industry is intensifying with key players adopting differing strategies to scale up production. The choice between large-scale green hydrogen plants and smaller, modular units represents two competing visions for the future of this critical clean energy source. The moot question is which of these approaches is better suited for quick green hydrogen adoption.
The strategy of building large-scale integrated electrolyser facilities is based on the belief that significant decarbonisation can only be achieved at scale. Those who follow this line of thought believes that decarbonising heavy industries like steelmaking, chemical production, and shipping requires substantial hydrogen production capacity, making small-scale solutions insufficient for these large-scale applications.
READ | Plastic pollution: How the throw-away culture snowballed into a crisis
Large-scale plants have clear advantages. Economies of scale can reduce the per-unit cost of hydrogen production, making it more affordable and accessible. Massive industrial sectors that require vast amounts of hydrogen, such as steel and chemicals, can be more effectively served by large-scale production. Furthermore, by designing all parts of the integrated plant, the inefficiencies and costs associated with piecemeal, bespoke engineering solutions can be avoided.
However, there are significant challenges. Securing the necessary funding for such large-scale projects can be difficult, with substantial risks involved in pioneering new technology at this scale. Additionally, large plants require extensive infrastructure, including transportation and storage systems, to handle the significant hydrogen output.
Case for modular green hydrogen units
Some other corporations are taking a different path by focusing on smaller, modular electrolyser units. The smaller electrolyser units can fit into a typical garage and are designed to be scalable, allowing customers to add capacity as needed. This flexibility enables the units to meet varying demand levels and locations efficiently.
Modular units offer several advantages. Their flexibility allows them to be deployed in diverse locations and scaled up incrementally, making them suitable for a wide range of applications, from small-scale industrial use to decentralised energy systems. Smaller units lower the initial capital investment required, making it easier for businesses and communities to start using green hydrogen. Additionally, modular systems can quickly adapt to changing market demands and technological advancements, offering a more dynamic approach to hydrogen production.
Despite these benefits, there are challenges. While modular units can be combined to increase capacity, they may not achieve the same economies of scale as large plants, potentially resulting in higher per-unit production costs. Convincing large industrial users and financiers to invest in smaller, less established technologies can also be challenging.
Technological and market considerations
Both the sides use proton exchange membrane (PEM) technologies, which are well-suited for integrating with renewable energy sources like wind and solar. This compatibility is crucial for producing truly green hydrogen. The choice between large and small electrolysers also involves considerations of efficiency, reliability, and ease of maintenance.
The demand for green hydrogen is expected to grow significantly, driven by government mandates, corporate sustainability commitments, and technological advancements. The International Energy Agency forecasts a need for nearly 100 million metric tons of clean hydrogen by 2030 to meet decarbonisation targets. This immense demand will require contributions from both large-scale plants and modular systems.
The debate between big green hydrogen plants and small modular units does not have a one-size-fits-all answer. Each approach has its merits and is likely to find its niche in the evolving hydrogen economy. Large-scale plants may dominate in serving heavy industries and centralised production hubs, while modular units offer flexibility and adaptability for decentralised and smaller-scale applications.
Ultimately, the development of a robust green hydrogen infrastructure will likely involve a combination of both strategies, tailored to meet the diverse needs of various sectors and regions. By leveraging the strengths of both large-scale and modular approaches, we can accelerate the transition to a cleaner, more sustainable energy future. The key to rapid green hydrogen adoption lies in understanding and utilising the complementary benefits of both large and small solutions, creating a hybrid model that can respond to the demands of today and tomorrow.