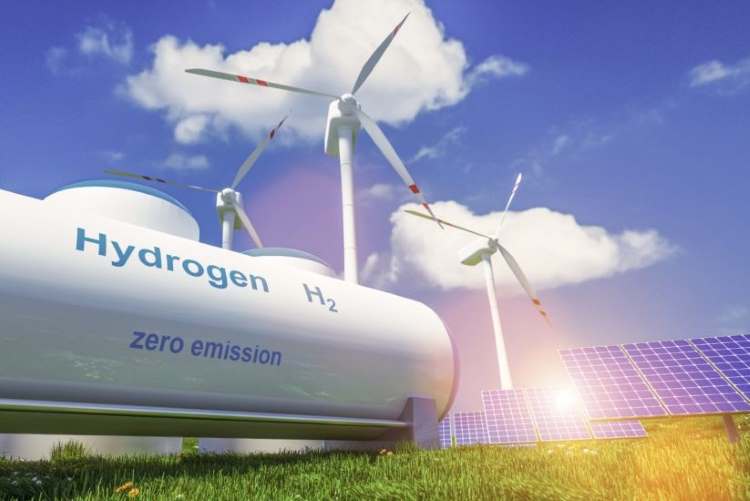
The world is looking at Green hydrogen as a clean fuel that van replace carbon fuels in the foreseeable future. There are many hurdles to achieving large-scale production of this clean fuel. These challenges are: the high cost of production, difficulties in storing and transporting hydrogen, and the low efficiency of electrolysers used to produce hydrogen by splitting water.
Several teams of scientists in advanced countries and China are currently working to find solutions to these problems. The world needs urgent action to develop technologies and processes that can reduce the cost of green hydrogen production and make it a viable alternative to carbons fuels.
The recent years have witnessed several breakthroughs that improved the efficiency of green hydrogen production. The most efficient electrolysers utilize polymer electrolyte membranes (PEM) that require electrodes containing iridium, a metal that is 2.5 times more expensive than gold. The scarcity of iridium is a major limiting factor for the green hydrogen industry, with annual global production standing at just 10 tonne.
READ I Climate finance: Need specialised institutions, innovative funding
Breakthrough in green hydrogen technology
A pioneering solution to this issue has been developed by the Japanese conglomerate Toshiba. They have devised a process that reduces the iridium requirement in PEM electrolysers by 90%, without compromising output and durability. This breakthrough catalyst, known as iridium oxide nanosheet, has the potential to significantly reduce electrolyser prices and facilitate the adoption of green hydrogen as a viable fuel.
According to Toshiba, their new technology could help Japan reduce the cost of green hydrogen from the current 100 yen per cubic meter to 20 yen by 2050. The technology is ready for commercialisation and could be rolled out without any delay, the company has announced.
Presently, the total installed capacity of electrolysers is approximately 1 GW. With the advent of this technological breakthrough, the world could exceed the projected capacity of 134 GW by 2030. Electrolysers using this revolutionary technology are expected to enter the market in the mid-2020s.
Another Japanese manufacturer, Toray, has developed an electrolyte membrane that utilizes hydrocarbons. This highly efficient membrane is claimed to be four times stronger than those currently used in electrolysers. By employing such a membrane, the cost of hydrogen production could be significantly reduced. Toray is currently conducting field tests on this membrane, with products incorporating it expected to hit the market by 2025.
Panasonic Holdings, another Japanese conglomerate, is conducting research on alkaline electrolysers that do not require expensive metals. Using nanotechnology, Panasonic aims to increase the efficiency of alkaline electrolysers, making green hydrogen even more affordable. This new technology is scheduled to enter trial phase in the next two years.
Scientists have made significant progress in reducing the energy industry’s reliance on rare metals, including iridium, in PEM electrolysis devices. Researchers at the Hydrogen and Fuel Cell Research Center of the Korea Institute of Science and Technology have achieved a breakthrough in reducing the requirement for iridium and other precious metals in electrolysers.
Researchers worldwide are actively involved in enhancing electrolyser efficiency, focusing on three key areas:
The development of new membranes is a primary focus for many researchers. Efforts are under way to create membranes that can withstand higher temperatures and pressures. Currently, membranes are typically made of Nafion, a polymer that degrades under high temperature and pressure. Researchers are working in developing more durable membranes, using materials such as ceramics and metals.
Researchers are also working to develop efficient electrocatalysts that could reduce energy consumption in the hydrogen production process. Electrocatalysts facilitate the reaction that splits water molecules to produce hydrogen. Platinum, a rare and costly material, is commonly used in electrocatalysts. However, researchers are working on new electrocatalysts that employ cheaper materials like nickel and cobalt.
Additionally, there are initiatives to redesign electrolyzes to make them modular and scalable to integrate them with renewable energy sources. The idea is to deploy electrolyzes at scale to take advantage of the intermittent nature of renewable energy sources.
China is the world’s leading producer of electrolysers. Its companies such as 718th Research Institute of CSIC, Beijing Hydrogen Energy, and Guodian Nanjing Hydrogen Energy leading the world in this sunrise industry. Germany has some of the leading electrolyser research and development institutions such as the Fraunhofer Institute for Solar Energy Systems. Japan and the United States also have powerful electrolyser manufacturing industries.