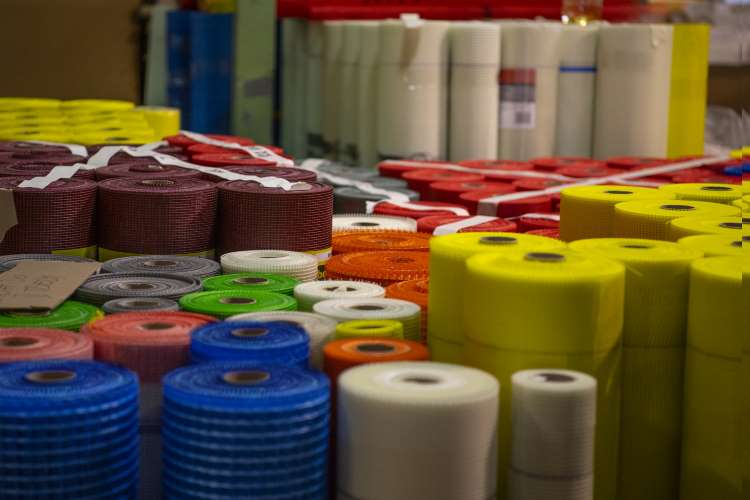
Inflation weighs on technical textiles industry: Two years into the pandemic, it looks like the uncertainties that emerged with the Covid-19 pandemic are here to stay longer than we anticipated. When Covid-19 emerged in February 2020, governments announced a number of measures to contain the spread of the pandemic. Such restrictions disrupted the movement of men and material across the globe and governments and citizens stockpiled food, medicines, and other critical supplies. Commodities gained strategic salience when self-reliance and supply chain resilience became core themes of organisational strategy.
Even before the pandemic emerged, a process of deglobalisation was gaining momentum, triggered by the US-China trade war. Governments had started pursuing inward-looking policies and businesses were under pressure to step up domestic production, create job opportunities locally, and reduce dependence on other countries. Covid-19 intensified the trends of onshoring and nearshoring where companies worked out strategies to bring back manufacturing of essential components within its borders. This insulated them from geo-political risks and disruptions like pandemics.
READ I The recession and aftermath: Five trends that will shape of the next cycle
Except for a few traditional industries and commodities, self-reliance was virtually impossible. For industries like technical textiles, some materials like polyester were available almost everywhere while some others like carbon fibers or high tenacity yarns had to be sourced from other countries. Another challenge was that the textile supply chain has several tiers of production. Identifying supply chain partners and activities is a major challenge that companies faced when they tried to catch up with the onshoring and reshoring trend. Beyond that, the cost of producing some components did not prove to be worthwhile.
The governments announced several measures to deal with the pandemic induced economic crisis. Steps such as quantitative easing fueled global demand. Companies were struggling to maintain the flow of funds, goods, services, and information in the supply chain. This led to shortages in both goods and labour supply, leading to unanticipated inflationary pressures. As per a report published by the Bureau of Labor Statistics in May 2022, the annual inflation rate measured by the consumer price index peaked at 8.6%, the highest since 1981.
READ I NSO data: Unemployment rate falls, but, women participation still lags behind
Technical textiles and energy prices
When the threat of pandemic was subsiding, the Russia-Ukraine war disrupted the supply chain operations and sent another round of shocks. What companies thought of as a one- time supply chain crisis stayed longer to affect all aspects of their operations. The disruptions in the energy sector due to the war are causing a ripple in the technical textile industry which is an energy intensive industry. The fluctuating oil prices had repercussions on the price of polyester and other textile fibers derived from it.
Energy commodity price index
The advent of new materials complemented by the versatility of the end-usage drives the success of the technical textiles industry. Technical textiles industry is a tech-dependent, research-centered sector and have found applications in various industries such as automotive, agriculture, shipping, healthcare, construction, defense and aerospace.
The global market for technical textiles is estimated to touch $208.5 billion by 2024 with Europe being the largest market with a share of more than 28%. During the period, Asia-Pacific is also expected to grow rapidly at a CAGR of 7.7%. Europe has a strategic advantage of being close to car manufacturers while in Asia-Pacific, China’s demographics drive its production and consumption abilities.
The global market for technical textiles evolves from a broad range of end-use sectors and is heavily dependent on the pace of technological transformation. Innovation spending is an essential determinant of the sustainability of companies involved in the manufacturing of technical textiles. A thick line that exists in terms of innovation investments and spending separates the traditional textiles and technical textiles industry. There is always a constant demand for new technical textile solutions to meet the evolving functional needs of industrial sectors such as automotive, healthcare, and sports goods.
Access to exclusive, proprietary technologies and technical expertise drives the industry and this comes at the cost of investments in the R&D. This is crucial at a time when the most-anticipated migration of the automotive industry from fossil fuels to electric vehicles is finally happening. Achieving circularity and sustainability in textiles has become a key point of concern. Development of green technologies and environment-friendly products are gaining prominence. All of these expand the scope of technical textiles.
For instance, the evolution of e-vehicles in the automotive sector drives the demand for the development of seat belts, air, bags, carpets, safe motor parts, and other mobiltech applications. The rise of a health-conscious consumer base post pandemic means a rise in demand for sportech products. The increasing awareness about personal hygiene may boost the demand for meditech products. So, at the global level, the technical textiles industry is at a critical point of inflection.
Dr S Viju, Associate Professor, PSG College of Technology, who is also part of the technical textiles product development team, rates face masks as among the most in demand products in the healthcare sector.
Stubbornly high inflation across the globe means the companies have little room to spend on innovation and R&D after meeting their sourcing and operational costs. It is only natural for companies to be motivated to mitigate their risks to the maximum possible extent. In their endeavor to ensure sustainability and make profits, companies have now started to redraw their resource allocation plans. They are looking beyond onshoring operations to source raw materials and key components from other countries that can supply them at low prices.
Technical textiles gained more prominence during the pandemic. India was importing N95 masks and PPE kits when the pandemic struck and demand rose heavily. The country emerged as the second-largest supplier of these products after China during the pandemic crisis. The government support to domestic manufacturers was crucial in this high-value market.
Inflationary pressures and raw material shortages are forcing the companies to investigate the possibilities of substitution with low-cost materials to stay competitive. This will, in turn, impact the quality of the output. The quantitative tightening measures adopted by countries across the world to contain inflation have posed challenges for companies accessing credit, and capital investments.
The prevailing inflation is not the typical one where people have too much money to buy the same amount of goods and services. It is more about the mismatch between demand and supply that led to shortages creating a ripple that entered several sectors of the economy. To meet the demand for fabrics, adequate cotton was not produced and not enough fertilizers were produced to meet the demand from cotton farmers.
When the lockdown economy emerged, demand patterns changed. When recovery happened, a new normal emerged where the demand had a very different pattern. With the escalation of the Russia-Ukraine conflict, the world is witnessing another pattern. Until a new normal emerges and the economy reaches an equilibrium that would essentially be very different from what we had before 2019, supply disruptions would remain a principal determinant of organisational strategies.
(Sumathi Chakravarthy is managing director, and Sindhu Bharathi senior research analyst at Infinite Sum Modelling LLC, Seattle, USA. Badri Narayanan Gopalakrishnan is the former head, Trade, Commerce and Strategic Economic Dialogue, NITI Aayog, Government of India.)
Dr Badri Narayanan Gopalakrishnan is Fellow, NITI Aayog. Views expressed are personal.