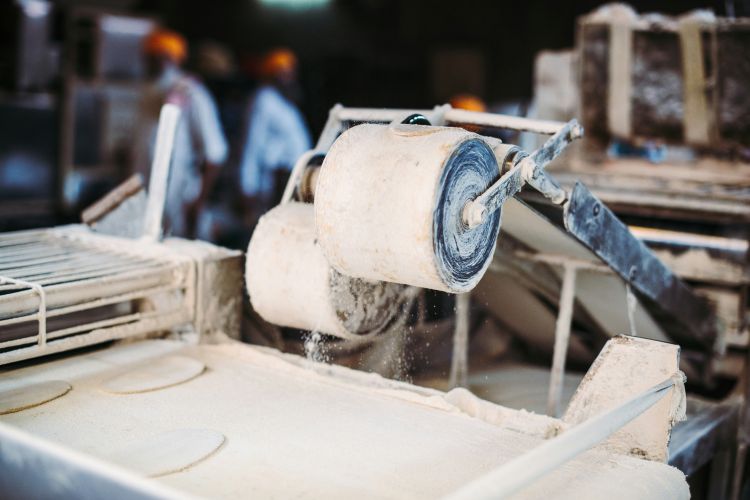
The ministry of heavy industry introduced the ‘Machinery and Electrical Equipment Safety (Omnibus Technical Regulation) Order, 2024, last month to align Indian safety practices with global standards. Set to take effect on August 28, 2025, this regulation mandates stringent safety standards for machinery and electrical equipment manufactured or imported into India. While the intention behind the new machinery safety standards is laudable — ensuring safer and globally compliant machinery — it is expected to significantly impact Indian manufacturers, particularly the micro, small, and medium enterprises (MSMEs) that make up 90% of the industry, says a study by GTRI, a New Delhi-based think tank.
The regulation will affect over 50,000 types of machinery, including industrial equipment such as pumps, compressors, cranes, and transformers. These essential machines fall under 463 tariff lines, and businesses that produce these goods will need to meet the stringent safety requirements laid out by the Bureau of Indian Standards (BIS). The Indian manufacturing sector, especially its MSME backbone, is underprepared to meet these new standards within the short timeframe provided. As a result, the one-year deadline is causing widespread concern among businesses that already operate with limited resources.
READ | GST Council may waive levy on health insurance
Key provisions of new machinery safety standards
Under the new machinery safety standards, all manufacturers will need to register with the Bureau of Indian Standards (BIS) and acquire a BIS standard mark or certificate of conformity. Compliance will be governed by three distinct safety standards: Type A, B, and C. Type A standards are general safety guidelines that apply to all machinery, focusing on design safety, hazard identification, and risk assessment. Type B standards cover generic safety requirements such as emergency stop functions and electrical safety across different types of machinery. The most specific, Type C standards, are machine-specific safety guidelines. When a conflict arises between the three types, Type C standards take precedence as they address unique safety needs for particular machinery.
This regulation is comprehensive, covering both machinery and parts or subassemblies. While it does not apply to machinery manufactured exclusively for export, this exemption provides little relief. Most companies manufacture goods for both domestic and export markets, meaning they will still need full BIS certification across their entire product range. The requirement for prior BIS approval for both production and imports will also likely delay the availability of essential machinery and equipment, creating bottlenecks in production.
Financial and technical challenges for MSMEs
The financial burden of complying with these new machinery safety standards is expected to be significant, especially for MSMEs. Compliance costs vary widely, with estimates ranging from Rs 50,000 to Rs 50,00,000, depending on the type and complexity of the machinery in question. This expense covers certification, safety upgrades, risk assessments, employee training, and the technical requirements to bring machinery up to standard. Given the already thin margins within which many MSMEs operate, such costs are prohibitive and may push some businesses toward closure.
Moreover, the technological gap is another significant hurdle for MSMEs. Many smaller firms do not have access to advanced machinery or technology capable of complying with the new standards. Retrofitting existing equipment or purchasing new machinery will require significant investment, which may be out of reach for smaller businesses. In addition to these financial constraints, MSMEs often lack the skilled workforce needed to implement the necessary safety measures. Hiring or training staff to meet Type A, B, and C standards will place an additional strain on already tight budgets, compounding the difficulty of compliance.
Another major challenge is the regulatory complexity itself. The technical language used in the order is difficult for smaller firms to navigate, and the lack of detailed implementation guidelines from BIS has only added to the confusion. MSMEs, which frequently operate with limited administrative resources, are struggling to understand how to comply with these multi-layered standards. Without clearer instructions, many firms remain unsure about how to proceed with the necessary upgrades.
Implications of the regulation
The impact of this regulation will be far-reaching. India’s imports of machinery and electrical equipment, which amounted to $25 billion in FY2024, could face delays as companies wait for BIS approval. With 39.1% of these imports coming from China, any delay could worsen supply chain bottlenecks, further slowing industrial growth. On the domestic front, manufacturers who cater to both the local and export markets will have to navigate the new compliance landscape, increasing the regulatory burden on an already stressed sector.
Although export-oriented machinery is exempt from the regulation, the reality is that most manufacturers produce goods for both domestic and international markets. This means that even businesses focused on exports will need to secure BIS certification for their entire product line. As a result, the exemption provides only limited relief, and manufacturers must comply with the same safety standards across the board.
A phased implementation strategy
To mitigate these challenges, a phased approach to implementation is essential. The current one-year timeline for compliance is simply too short, particularly for MSMEs that lack the financial and technical resources to meet the stringent safety standards. Extending the deadline to allow MSMEs more time to adapt would be a more realistic and equitable solution. A three-year timeline for meeting Type A standards and an additional five years to comply with Type B and C standards would offer businesses the breathing room they need. This approach mirrors the phased regulatory models used in other countries, such as the European Union, where industries are often given five to seven years to transition to new safety standards.
Moreover, implementing the standards in phases based on the complexity and risk level of the machinery would allow firms to prioritise safety upgrades without jeopardising their operations. For example, horizontal safety standards (Type A) could be enforced first, followed by vertical (Type B and C) standards as businesses gain the technical and financial capacity to comply. The medical devices industry in India provides a useful example, where voluntary registration was initially encouraged, followed by mandatory standards based on the risk level of the device. This model could be adapted for the machinery sector, providing a more manageable path toward compliance.
Government support will also be crucial in helping MSMEs meet these new safety standards. Financial assistance in the form of subsidies or low-interest loans could help smaller firms afford the necessary upgrades to their machinery. Additionally, the government should conduct awareness campaigns and training programs to educate businesses on the importance of these regulations. Establishing a dedicated helpdesk to guide MSMEs through the certification process would also alleviate much of the confusion and help streamline compliance efforts.
Finally, certifying a pool of technical professionals who can assist industries in implementing these standards is essential. MSMEs often lack the expertise needed to navigate such complex regulations, and without access to trained consultants, many businesses will struggle to meet compliance requirements. Industry associations can play a pivotal role in this regard by negotiating bulk certification agreements, conducting training sessions, and providing technical guidance to MSMEs. These associations are ideally placed to bridge the gap between government regulations and industry readiness, ensuring a smoother transition for smaller firms.
The Machinery and Electrical Equipment Safety (Omnibus Technical Regulation) Order, 2024, represents a necessary step toward improving manufacturing safety in India. However, the challenges facing MSMEs in complying with these new regulations are substantial. A phased approach to implementation, combined with targeted government support, will be essential to ensuring that the benefits of these new regulations are fully realised without unduly burdening the sector that forms the backbone of Indian manufacturing.